A metal bracket is an intermediate metal component used for fixing one part to another, e.g., a shelf to a wall. In addition to creating a connection between two parts, a metal bracket can be used to provide support. Metal brackets consist of two or more planes connected along one edge. The simplest and most common way to fabricate this object is to bend a flat object in two or more positions. Read More…
We are the metal stampings experts. We have over 30 years of experience creating customized solutions for our customers in a wide variety of industries. We are fully 9001:2008 certified, and we bring that high quality commitment to everything we do.

Manufacturer of precision metal stampings for the automotive, electronics, electrical, medical, industrial & consumer markets.
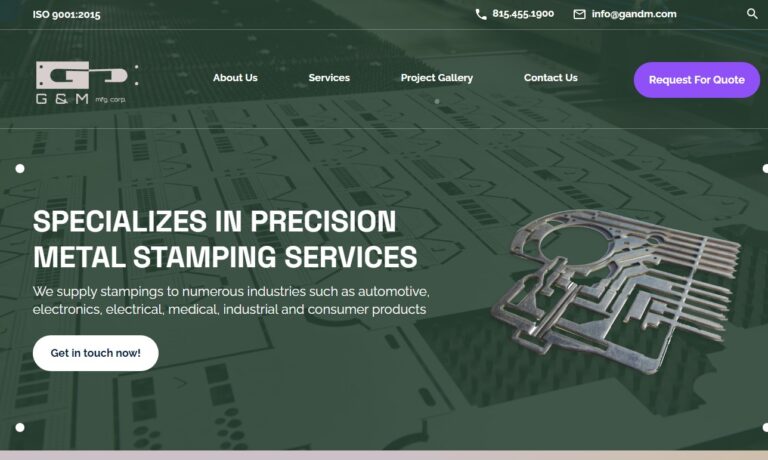
As a premiere metal stamping company in the United States, we are fully capable of producing the engineered products you need to get to get your job done.

At Pacific West America, Inc. we provide custom metal stamping, CNC machining, printed circuit boards, and membrane switches. Utilizing state of the art machinery, we offer precision metal fabrication and sheet metal fabrication. The company consists of two state-of-the-art plants, staffed with highly trained engineers and experts prepared to handle all of your projects. For unparalleled service...
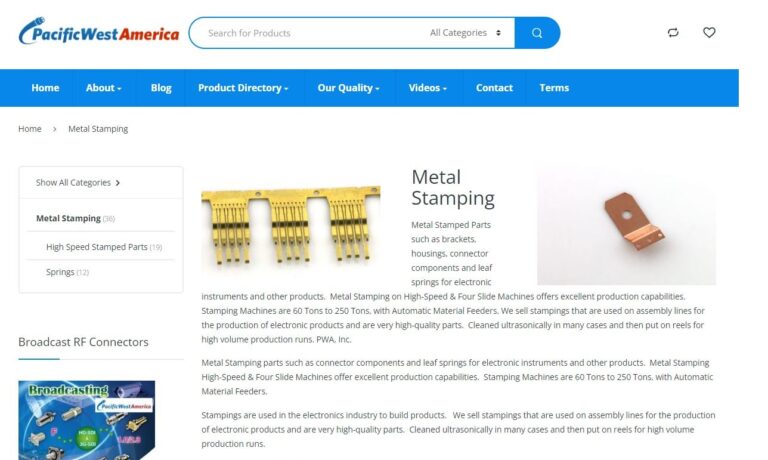
Apex Spring & Stamping is a certified minority owned company that manufacturers springs, stampings, wire forms, clips, and fasteners. Our core industries include automotive, office furniture, medical, recreational, consumer goods, and appliances. We also specialize in value added assembly and prototyping. Our engineering team will ensure your part is both functional and cost-effective. IATF 16949 ...

We perform medium to large quantities of precision metal stamping and commercial metal stampings. We do our tooling design in house using the latest CAD machinery. We also offer other in house services like tapping, spot welding, arc welding, and assembly of products.

Quality Stamping & Tube Corp has been a leader in the aluminum extrusions and metal stamping industries for over 40 years. We attribute our success to our in-house die-making capabilities and wide range of extruded parts. All of our products are manufactured with quick turnaround and made to be high quality and durable. Our metal stampings can be up to 1/4 inch thick with various metals,...
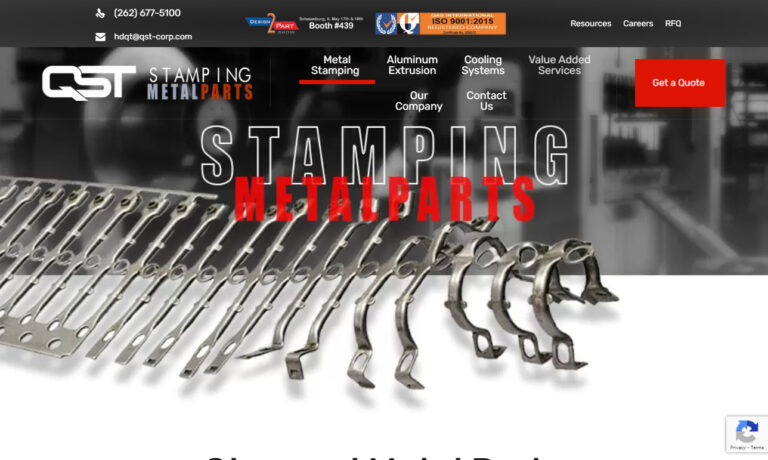
At Serra Manufacturing Corporation, we take great pride in our position as a leading manufacturer of precision-engineered metal stampings. With a relentless commitment to quality, we have established ourselves as a trusted partner in the metal stamping industry. Allow us to introduce you to our extensive product offerings, comprehensive services, and our unwavering dedication to delivering...

More Metal Bracket Companies
The easiest machining method would be to add a 90° bend to a flat rectangle with a straight profile, turning it into a metal bracket with an L-shaped profile. Metal brackets can support objects like countertops, shelving, mounted televisions, and furniture sections. Metal brackets can be stamped from various materials such as brass, copper, aluminum, and stainless steel. The metal brackets can also be coated with a variety of materials to enhance their appearance. The application of the metal bracket will affect the type of material it is stamped from, the shape, and the appearance.

How Brackets Are Made
Metal brackets can be made in various ways, which include casting or CNC machining. However, the ideal way to make brackets is by sheet metal fabrication. One of the processes commonly used for sheet metal fabrication is bending. In this process, a machine called a bend is used to bend sheet metal to an angle up to 120°. This process is important since all brackets virtually incorporate at least one bend. Before any sheet bending process occurs, the sheet metal must be cut to size using a machine such as a plasma cutter or a laser cutter. A punching machine may be used to make holes in the bracket for fitting screws. Welding is also required in the addition of gussets or other related features.
Types of Metal Brackets
Bracket varieties vary based on the application and the objects they are designed to support. Some of the configurations for metal brackets include L-brackets, J-brackets, Box brackets, U-brackets, Z-brackets, and gusset brackets. J-brackets are used in construction and often in automotive applications. They can also be found in structural applications in conjunction with L-brackets. Box brackets are also named square brackets, and these are one of the strongest types of metal brackets.
L-Bracket
An L-bracket is one of the commonly used bracket types. The L-bracket contains an L-shaped profile after being bent along a single axis, creating a 90° angle at most. The L-bracket is used in many applications where a horizontal object needs mounting to a vertical object.

This scenario may be seen in mounting a shelf to a wall. The L-bracket is widely used in decorative and structural applications.
U-Bracket
Unlike the L-bracket, the U-bracket is bent along two axes, forming a U-shaped profile. The U-brackets can be used to grip an object between its flanges or mount two horizontal parallel objects above the other.

Z-Bracket
A Z-bracket is a type of metal bracket that incorporates two bends. However, unlike a U-bracket in which two bends are formed on the same face of the metal sheet, the Z-bracket bends one flange inwards and the other outwards to make a Z-shaped profile. As a result, the Z-brackets can be used to mount surfaces that are parallel and offset from one another.

Gusset Bracket
The gusset bracket is a metal bracket supported with extra material to improve its load-bearing capacity and strength. The gusset bracket is like an L-bracket but with an extra triangular section of material between the horizontal and vertical sections.

The gussets can be welded onto the bracket or included within a single piece. In the latter, the vertical and horizontal faces of the bracket are bent from the edges of the triangle.
Applications and Uses of Metals Brackets
Metal brackets are often used for decorative purposes. In decorative applications, the metal brackets can be powder coated in colors such as white, gray, etc., to be more aesthetically pleasing. Metal brackets can be used in the telecommunications, electronics, construction, automotive, defense, commercial, dental, architecture, and aerospace industries.
Choosing the Right Metal Brackets Manufacturer
To make sure you have the most positive outcome when purchasing Metal Brackets from a Metal Brackets Manufacturer, it is important to compare at least 5 or 6 Manufacturers using our list of Metal Brackets suppliers. Each Metal Brackets Supplier has a business profile page that highlights their areas of experience and capabilities and a contact form to directly communicate with the manufacturer for more information or request a quote. Review each Metal Brackets business website using our patented website previewer to get an idea of what each business specializes in, and then use our simple RFQ form to contact multiple Metal Brackets companies with the same form.